Precision pH Control for Industrial Wastewater:
LibertyCES Solves Dosing Challenges at Major U.S. Cheese Plant
LibertyCES engineered a high-precision electric chemical dosing system that eliminated overshooting, reduced chemical waste, and ensured EPA compliance — all while keeping operations uninterrupted.
📞 Talk to an Engineer
Stabilizing Wastewater pH for a U.S. Cheese Processor
❌ The Challenge: Unstable pH & Chemical Overuse
- No pH Sensor Feedback made corrections guesswork-based.
- Overshooting due to batch flow swings and lag time.
- Fouled Probes delayed dosing cycles.
- Manual Dosing caused 18–25% acid & caustic overuse.
- Title 22 Violations risked permit compliance (pH 6.0–9.0 limits).
Keywords: food plant wastewater treatment, fouled sensors, pH correction automation
✅ The Solution: Smart Dosing + Real-Time PLC
- Closed-Loop Logic enabled real-time dosing via PLC.
- Inline pH Sensors eliminated overshoot corrections.
- Electric Pumps delivered low-flow precision control.
- SCADA Integration ensured continuous data-driven feedback.
- 24% Chemical Savings in both sulfuric acid and KOH usage.
Result: No compliance violations, scalable automation, 6–8 hours/week saved.
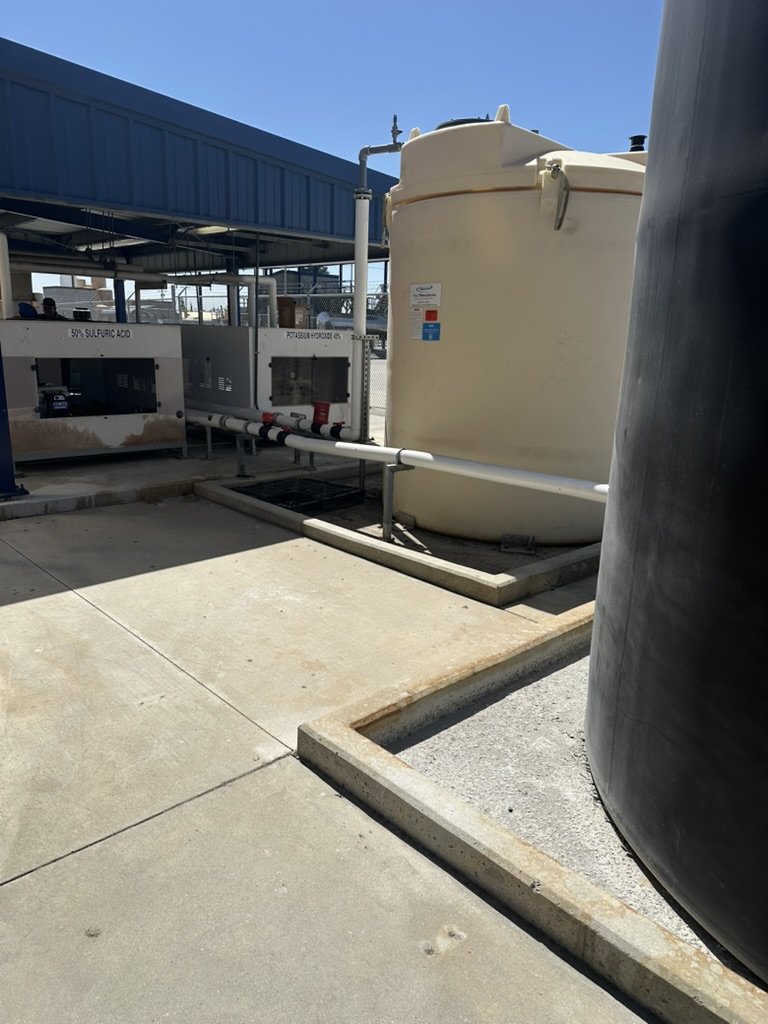
Graco Quantm i30 dosing cabinet automated pH control — reducing waste and restoring EPA compliance.
Real-Time pH Stabilization for Industrial Acid Injection
A U.S. food processor was injecting 50% sulfuric acid and 45% potassium hydroxide into 125,000-gallon tanks — blindly, without sensor logic. Overshooting and chemical waste were unavoidable.
With LibertyCES and the Graco QUANTM™ electric diaphragm system, chemical dosing is now controlled by inline sensor data and real-time PLC logic — adapting dynamically to flow conditions.
- ✔️ Reduced overshoot & pH drift
- ✔️ Dynamic response to batch flow
- ✔️ Full SCADA integration
- ✔️ 24% improvement in chemical efficiency
Automation turned trial-and-error into 24/7 chemical intelligence.
🔧 LibertyCES Inline Hardware Stack
The exact configuration used to dose 50% sulfuric acid and 45% caustic across a 125,000 GPD wastewater system—no surge, no error, full compliance.

Graco QUANTM™ i30 Pump
Electric diaphragm dosing from 1–90 GPM. Ultra-low pulsation, safe for inline pH control of 50% sulfuric acid.
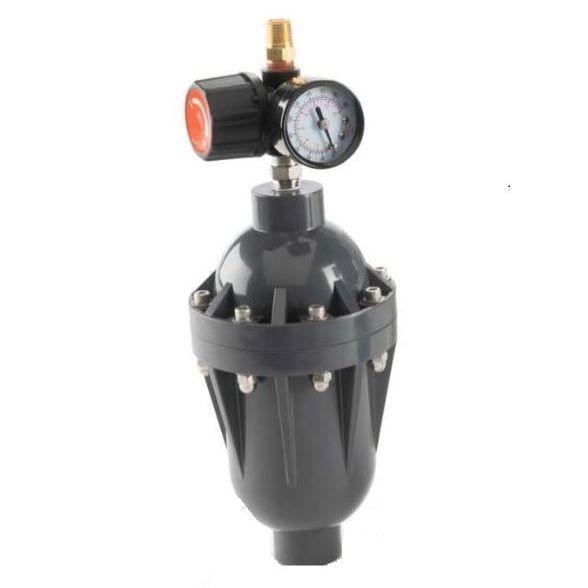
Griffco Pulsation Dampener
Smooths discharge pulses to protect sensors and stabilize dosing—especially critical at low flow rates.

Plast-O-Matic Gauge Guard
PTFE-lined housing isolates sensitive instruments from chemical shock, extending service life in acid-heavy systems.
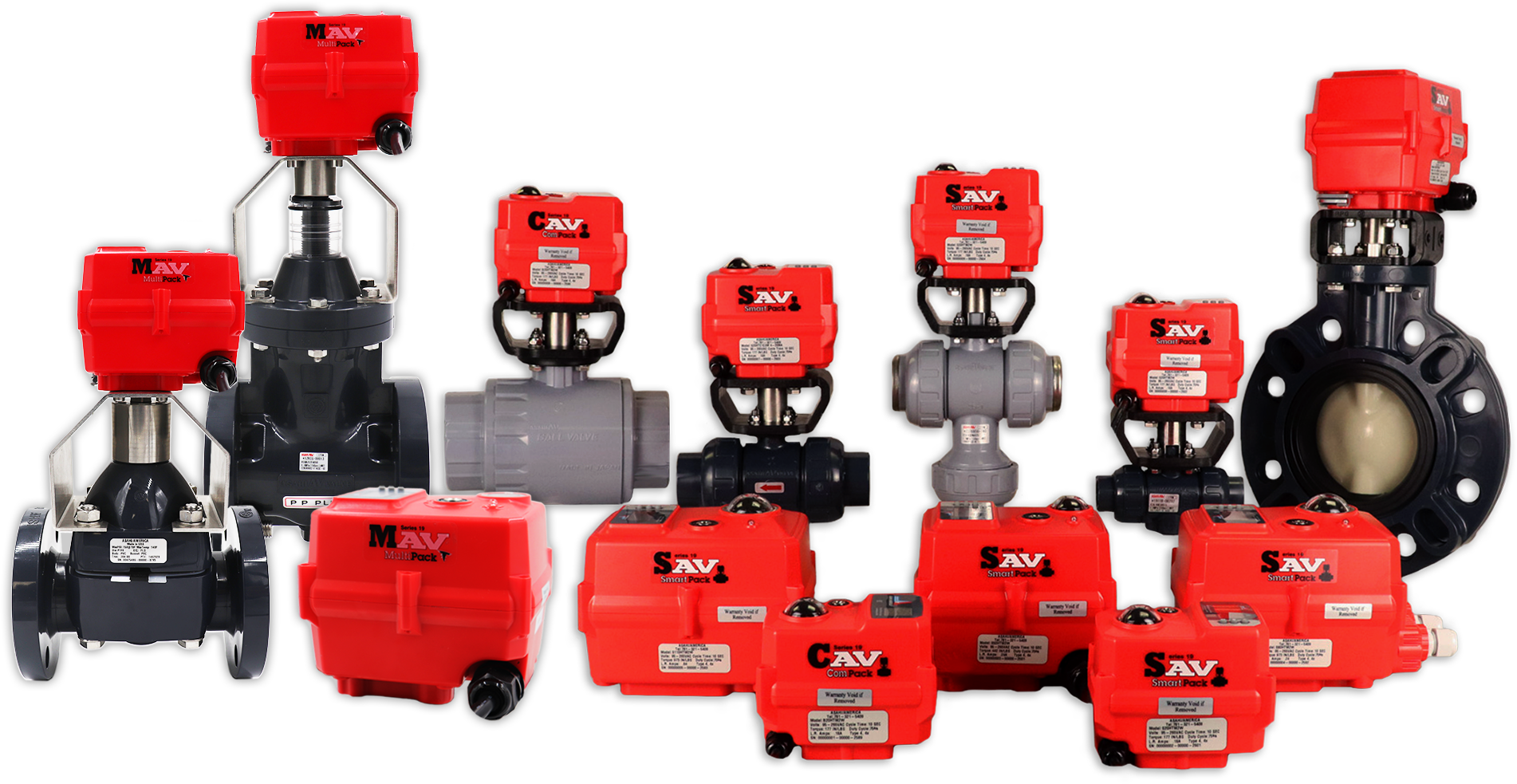
Asahi Series 19 Valve
Electrically actuated PVC valve provides remote isolation of chemical flow during sensor lockout or logic override.
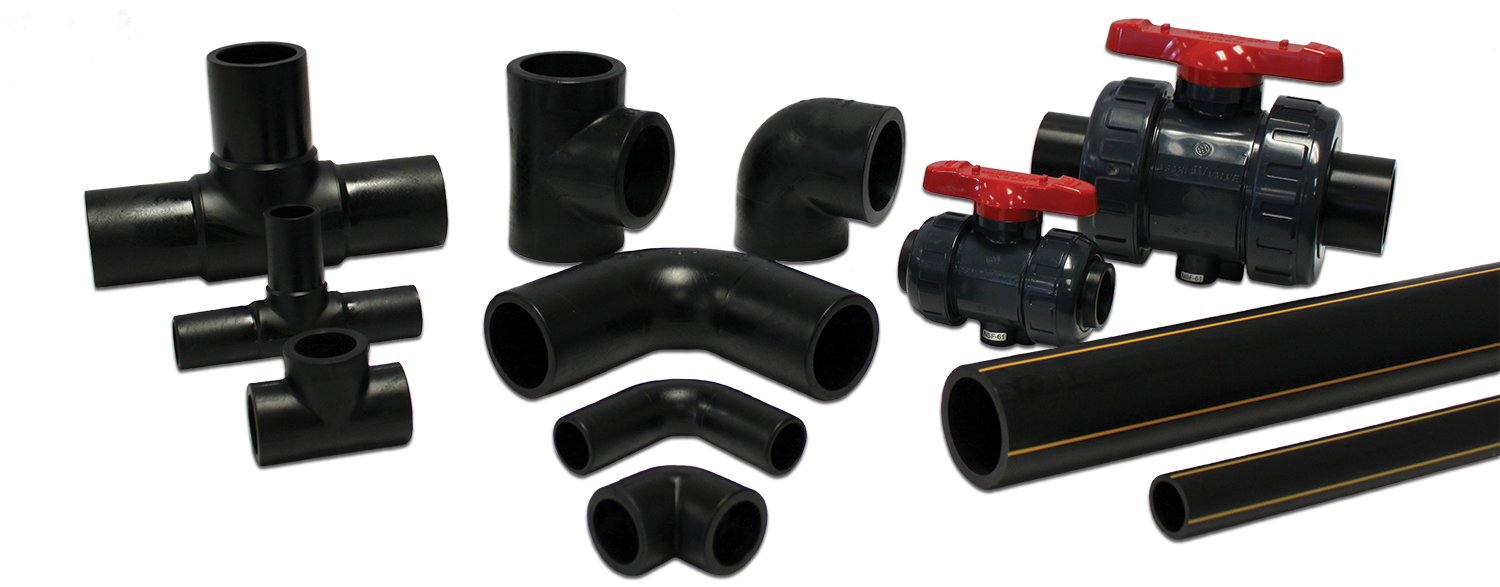
Asahi ChemProline™ Piping
Butt-fused HDPE piping rated for sulfuric, hydrochloric, and caustics. Integrated PVC valves for tight routing.
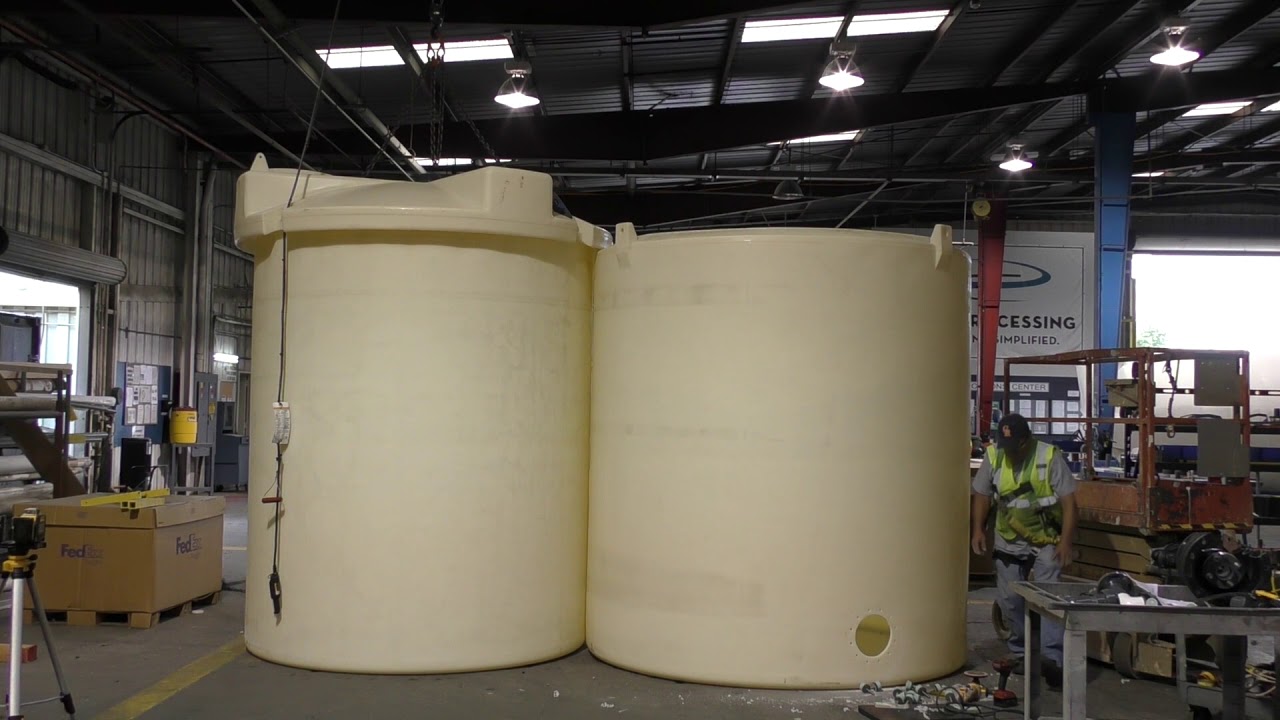
Poly Processing SAFE-Tank®
Double-wall XLPE tank system with internal secondary containment. No sump, no concrete, no compromise.